Enhancing Equipment Performance: The Key Role of a Well-Managed Maintenance Database
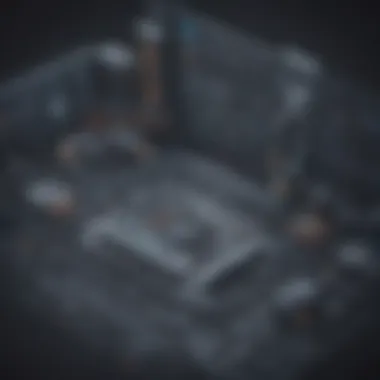
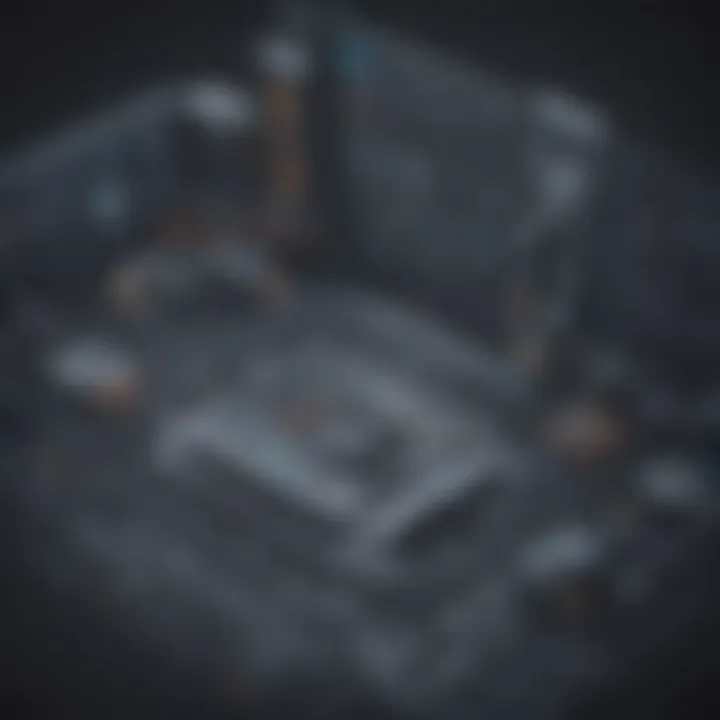
Software Overview and Benefits
Pricing and Plans
When considering the implementation of software for optimizing equipment performance through an efficient maintenance database, analyzing the pricing structure and available plans is essential. The pricing of the software should align with the budgetary constraints of the organization while offering competitive features and benefits. Comparing the pricing with other software solutions in the same category is crucial to ensure cost-effectiveness and optimal value for investment. By understanding the pricing and plans available, businesses can make informed decisions that benefit their maintenance database management strategies.
Performance and User Experience
The performance of the selected software in terms of speed, reliability, and user interface significantly influences its effectiveness in maximizing equipment performance. A software solution that exhibits fast processing speeds, high reliability in data management, and a user-friendly interface enhances operational efficiency and user satisfaction. User experience insights and feedback on usability play a vital role in assessing the software's suitability for maintaining an efficient maintenance database. Evaluating the performance and user experience aspects thoroughly helps businesses select software that fulfills their requirements seamlessly.
Integrations and Compatibility
Exploring the integrations offered by the software is critical to ensuring seamless connectivity with other tools and platforms utilized in the organization. The software's compatibility with different operating systems and devices determines its adaptability within the existing technological ecosystem. Assessing the level of integrations and compatibility helps businesses integrate the software effectively into their maintenance processes and systems, enhancing overall operational efficiency and data management capabilities.
Support and Resources
Introduction
In the realm of industrial operations, maintaining equipment plays a pivotal role in ensuring seamless functionality and operational efficiency. This article delves into the critical aspects of cultivating a well-organized equipment maintenance database. By embracing effective database management practices, businesses can streamline maintenance protocols, diminish downtime occurrences, and lengthen the operational lifespan of their machinery. The exploration of strategies for establishing, enriching, and utilizing an equipment maintenance database serves as a cornerstone to boosting overall operational efficiency and productivity.
Understanding the Significance of Equipment Maintenance
Equipment maintenance forms the bedrock of dependable operational performance. One of the critical facets under this umbrella is minimizing downtime. Efforts geared towards minimizing downtime serve as a linchpin for uninterrupted operational continuity. With a focus on this aspect, businesses can mortise time wastage and optimize production momentum through proactive maintenance measures. The efficiency of minimizing downtime lies in its ability to curtail productivity intermission, hence elevating the overall efficacy of maintenance strategies.
On the other hand, ensuring safety compliance is paramount in the landscape of equipment maintenance. The obligation to adhere to stringent safety protocols serves as a safeguard mechanism against potential hazards or operational lapses. By meticulously ensuring safety compliance, organizations nurture a secure working environment while mitigating risks and liabilities associated with equipment malfunctions or operational oversights. The vigilance toward safety compliance amplifies the reliability and dependability of maintenance procedures within the operational spectrum.
Enhancing equipment longevity stands as a testament to fruitful maintenance practices. By extending the lifespan of equipment assets, organizations curtail frequent overhauls or replacements, thereby slashing operational costs significantly. Proactively integrating measures to enhance equipment lifespan reflects a proactive stance towards resource optimization and sustainable operational practices. The diligence in fostering equipment longevity translates into sustained operational reliability and fiscal prudence within the organizational framework.
Role of Maintenance Databases in Modern Organizations
In the contemporary milieu of organizational dynamics, maintenance databases pinpoint the apex of streamlined data management systems. Centralized data management emerges as a cornerstone element in orchestrating information coherence across multifaceted maintenance operations. This centralized approach not only eases data accessibility but also harmonizes data utilization for informed decision-making processes. The essence of centralized data management underscores efficiency and accuracy in data-driven maintenance initiatives.
The advent of predictive maintenance capabilities revolutionizes the maintenance landscape by prognosticating equipment anomalies even before they materialize. This preemptive approach empowers organizations to preclude potential breakdowns through data-driven insights, thereby fostering a proactive maintenance ethos. Predictive maintenance capabilities not only optimize equipment performance but also reduce operational uncertainties, threading a path towards uninterrupted operational fluidity.
Furthermore, cost-effective resource allocation exemplifies prudent financial stewardship within maintenance undertakings. By leveraging cost-effective resource allocation strategies, organizations optimize resource utilization without compromising maintenance quality. This judicious balance between fiscal prudence and operational excellence sets the stage for sustainable maintenance practices, anti-gelling business longevity with prudent financial acumen.
Setting Up an Equipment Maintenance Database
Setting up an equipment maintenance database is a critical aspect of maximizing equipment performance through efficient maintenance practices. This section highlights the key considerations and benefits associated with establishing a robust database system for maintenance purposes. By focusing on selecting the right database system, businesses can enhance operational efficiency, reduce downtime, and prolong equipment lifespan.
Choosing the Right Database System
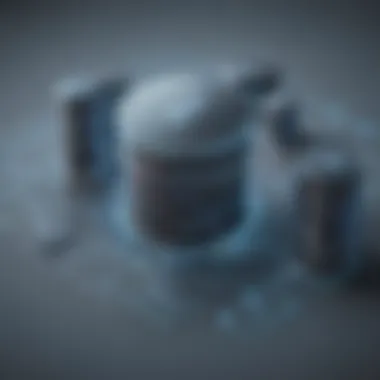
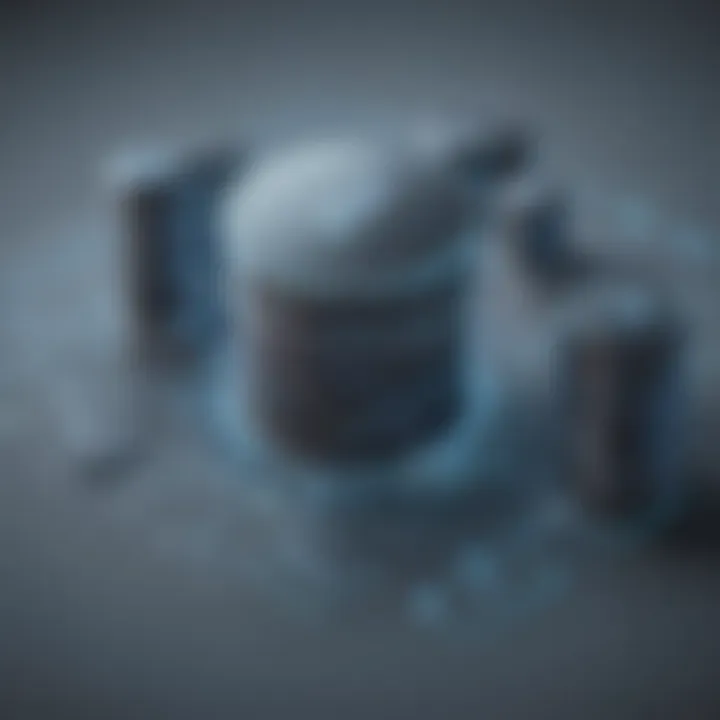
Selecting the appropriate database system is fundamental to the success of any maintenance initiative. Considerations for selection involve evaluating factors such as the system's compatibility with existing infrastructure, user-friendliness, and scalability. Opting for a database system that offers customizable features tailored to the organization's specific needs can significantly boost efficiency and streamline maintenance processes. One popular choice in this regard is a cloud-based database system, known for its accessibility, real-time updates, and cost-effectiveness.
Considerations for Selection
When deliberating on the selection of a database system, prioritizing features like user interfaces, data security measures, and integration capabilities can prove advantageous. The ability to seamlessly integrate the database with other systems and technologies within the organization contributes to a more cohesive maintenance workflow. Additionally, selecting a system that allows for easy data migration and backups enhances the overall reliability and resilience of the database.
Scalability and Flexibility
Scalability and flexibility are pivotal aspects of a database system, particularly in the context of maintenance operations. A system that can scale up or down based on evolving business needs ensures adaptability and long-term viability. Flexibility in terms of customization options and data handling enables organizations to tailor the database to their unique requirements, promoting a more efficient and effective maintenance framework.
Database Design and Structure
Efficient database design and structure lay the foundation for a well-organized maintenance database. Defined data fields, established relationships between data entities, and ensuring data integrity are key components of a structurally sound database system.
Defining Data Fields
Data fields that clearly categorize information related to assets, maintenance procedures, and historical records are essential for streamlined data management. By defining specific data fields for each type of information, users can easily navigate and extract relevant data, facilitating informed decision-making and proactive maintenance strategies.
Establishing Relationships
Establishing relationships between different data entities within the database enhances data connectivity and accessibility. By structuring relationships based on logical dependencies and associations, the database can provide a comprehensive overview of maintenance activities, asset interdependencies, and performance metrics. This relational approach fosters a holistic understanding of equipment maintenance within the organization.
Ensuring Data Integrity
Data integrity measures safeguard the accuracy and consistency of information stored in the database. By implementing validation rules, data encryption methods, and access controls, organizations can mitigate the risk of data errors, unauthorized access, and system breaches. Ensuring data integrity is crucial for maintaining the reliability and credibility of the maintenance database.
Populating the Database with Essential Information
Populating the maintenance database with essential information is a vital step towards enhancing maintenance operations. Detailed asset identification, comprehensive maintenance schedules, and thorough repair history records contribute to a comprehensive database structure.
Asset Identification
Accurate asset identification involves assigning unique identifiers to each piece of equipment within the database. This facilitates asset tracking, inventory management, and performance monitoring, enabling maintenance teams to swiftly locate and work on specific assets as needed.
Maintenance Schedules
Maintenance schedules outline planned maintenance activities, inspection routines, and service intervals for different equipment assets. By structuring detailed maintenance schedules within the database, organizations can proactively manage maintenance tasks, anticipate resource requirements, and optimize maintenance workflows based on predefined timelines.
Repair History Records
Maintaining comprehensive repair history records within the database enables insights into equipment performance trends, recurring issues, and repair effectiveness. Tracking repair activities, associated costs, and outcomes allows organizations to fine-tune their maintenance strategies, identify areas for improvement, and prioritize preventive measures to prolong equipment lifespan.
Utilizing the Maintenance Database Effectively
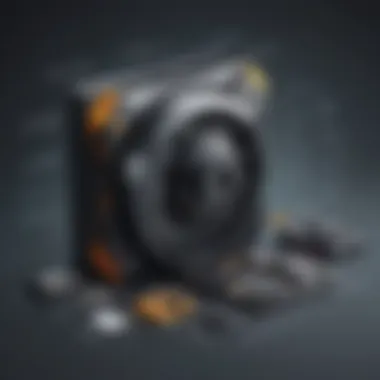
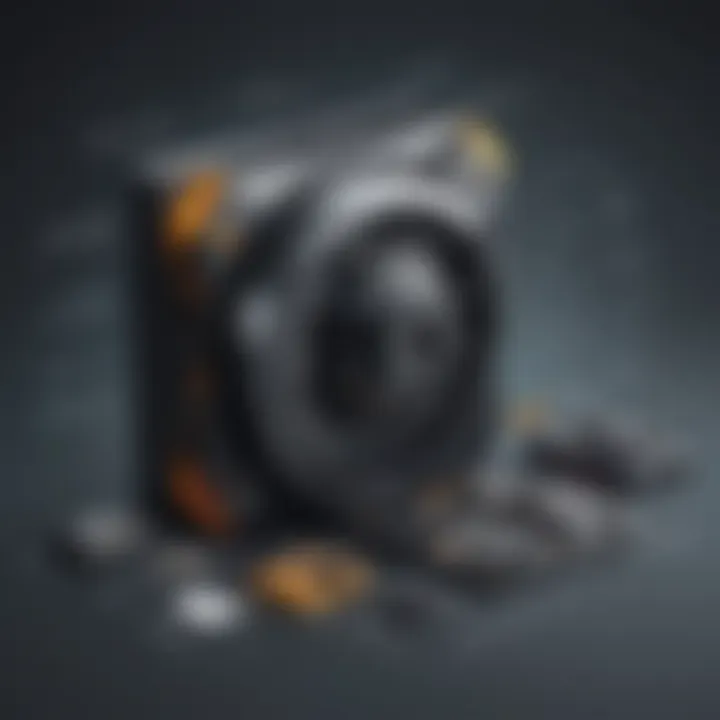
Utilizing the maintenance database effectively is crucial in optimizing equipment performance through an efficient maintenance database. By implementing preventive maintenance strategies and integrating IoT and sensor technologies, organizations can streamline maintenance processes, reduce downtime, and extend equipment lifespan. The ability to efficiently analyze maintenance data for continuous improvement further enhances operational efficiency and productivity.
Implementing Preventive Maintenance Strategies
- Creating Maintenance Tasks:
Creating Maintenance Tasks:
Creating maintenance tasks involves establishing a systematic approach to managing equipment upkeep. It plays a pivotal role in proactively addressing maintenance needs, thereby minimizing unexpected breakdowns and disruptions. The key characteristic of creating maintenance tasks lies in its ability to schedule routine checks and repairs in a structured manner, ensuring thorough equipment maintenance. This approach is widely favored for its proactive nature, allowing organizations to stay ahead of potential issues and avoid costly downtimes. However, while beneficial, creating maintenance tasks requires careful planning and allocation of resources to ensure optimal effectiveness.
- Scheduling Regular Inspections:
Scheduling Regular Inspections:
Scheduling regular inspections is instrumental in maintaining equipment in prime operating condition. This practice involves setting up recurring assessments to identify and address any emerging issues promptly. The main feature of scheduling regular inspections is its capacity to detect potential problems early on, preventing major breakdowns and enhancing equipment reliability. It is a popular choice for this article due to its preventive nature, which aligns with the overall goal of maximizing equipment performance through proactive maintenance. Nevertheless, scheduling regular inspections necessitates dedicated personnel and time commitments to uphold its benefits.
- Monitoring Equipment Performance:
Monitoring Equipment Performance:
Monitoring equipment performance is essential for ensuring that machinery operates optimally. This aspect involves real-time tracking of key performance indicators to gauge equipment efficiency and identify deviations from standard operation. The unique characteristic of monitoring equipment performance is its ability to provide actionable insights into equipment health and performance trends. It is favored in this article for its role in enabling data-driven decision-making and timely interventions to prevent potential failures. Nonetheless, monitoring equipment performance requires reliable monitoring tools and skilled personnel to interpret data accurately and derive meaningful conclusions.
Integrating IoT and Sensor Technologies
- Real-Time Data Collection:
Real-Time Data Collection:
Real-time data collection involves gathering operational information instantly through connected sensors and IoT devices. It contributes significantly to this article by enabling organizations to access up-to-date data for maintenance decision-making. The key feature of real-time data collection is its capacity to provide immediate insights into equipment status and performance metrics. It is a beneficial choice due to its timeliness in flagging potential issues and optimizing maintenance schedules. However, while advantageous, real-time data collection requires robust data infrastructure and secure networks to ensure data accuracy and reliability.
- Predictive Maintenance Alerts:
Predictive Maintenance Alerts:
Predictive maintenance alerts are proactive notifications triggered by data analysis algorithms to prompt pre-emptive maintenance actions. Their crucial role in this article lies in their ability to forecast equipment failures based on predictive algorithms. The standout feature of predictive maintenance alerts is their capability to prevent unplanned downtime by alerting maintenance teams to take preventive measures. They are a popular choice for their preventive maintenance approach and cost-saving potential. Nevertheless, leveraging predictive maintenance alerts effectively necessitates advanced data analytics capabilities and integration with existing maintenance systems.
- Automation of Work Orders:
Automation of Work Orders:
Automation of work orders involves streamlining the generation and assignment of maintenance tasks through automated processes. Its contribution to this article is in enhancing operational efficiency by expediting maintenance workflows. The key characteristic of automation of work orders is its capacity to reduce manual intervention in task allocation, improving overall maintenance process efficiency. It is a favored choice for its time-saving benefits and reduction of human error in work order management. However, implementing automation of work orders successfully requires seamless integration with existing database systems and proper training for personnel to adapt to automated workflows effectively.
Analyzing Maintenance Data for Continuous Improvement

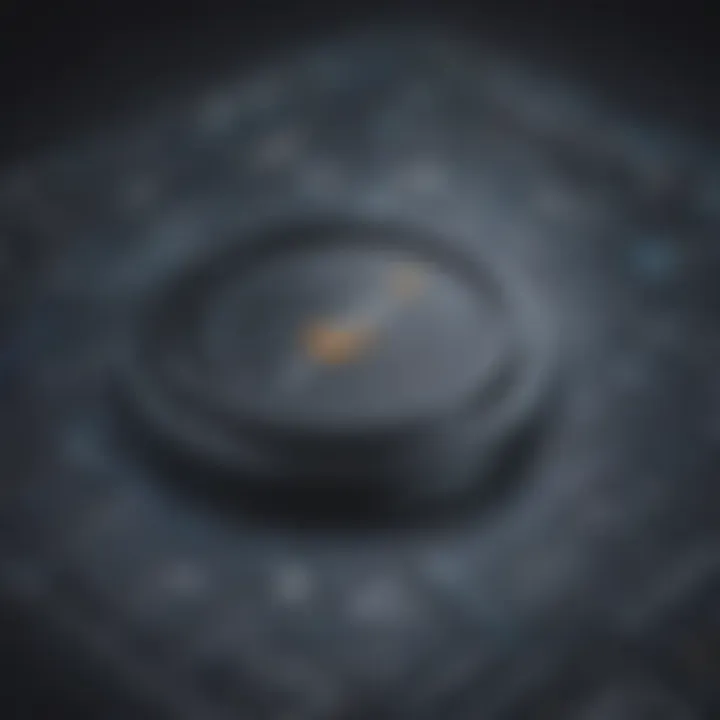
- Identifying Failure Patterns:
Identifying Failure Patterns:
Identifying failure patterns involves scrutinizing maintenance data to recognize recurring issues and failure trends. This practice significantly contributes to this article by enabling proactive maintenance actions based on historical failure patterns. The key characteristic of identifying failure patterns is its potential to forecast and prevent future breakdowns through targeted maintenance interventions. It is a popular choice for its preventive maintenance capabilities and long-term cost savings. However, effectively identifying failure patterns mandates sophisticated data analysis tools and skilled data interpretation to derive actionable insights accurately.
- Optimizing Maintenance Strategies:
Optimizing Maintenance Strategies:
Optimizing maintenance strategies entails refining existing maintenance processes to enhance efficiency and effectiveness. Its relevance to this article lies in its ability to fine-tune maintenance activities based on data-driven insights. The unique feature of optimizing maintenance strategies is its focus on continually improving maintenance workflows and resource allocation for better equipment performance. It is favored for its potential to reduce maintenance costs and enhance overall operational efficiency. Nonetheless, achieving optimal results from optimizing maintenance strategies requires a strategic approach and a willingness to adapt to changing maintenance needs.
- Implementing Performance Enhancements:
Implementing Performance Enhancements:
Implementing performance enhancements involves deploying innovative solutions to boost equipment functionality and longevity. This aspect contributes to this article through its emphasis on incorporating technological advancements to optimize equipment performance. The distinctive aspect of implementing performance enhancements is its capacity to drive continuous innovation in maintenance practices for sustained operational excellence. It is a beneficial choice for organizations looking to stay ahead of the curve in equipment maintenance and performance optimization. However, implementing performance enhancements effectively demands a forward-thinking mindset and a readiness to invest in emerging technologies for long-term benefits.
Benefits of a Well-Maintained Database
A well-maintained database is the backbone of efficient equipment performance in any organization. It serves as a repository of critical information that aids in minimizing downtime, ensuring safety compliance, and extending the longevity of equipment. By embracing a proactive approach to maintenance through regular database updates, organizations can significantly enhance their operational efficiency. The centralized data management offered by a well-maintained database allows for easy access to crucial information, facilitating informed decision-making and enhancing overall productivity. Utilizing advanced predictive maintenance capabilities, businesses can preemptively address potential equipment issues, resulting in cost-effective resource allocation and streamlined maintenance procedures.
Enhanced Operational Efficiency
Reduced Downtime
Reducing downtime is a pivotal aspect of maintaining operational efficiency within an organization. By swiftly addressing equipment failures and having access to historical maintenance data through a streamlined database, businesses can mitigate delays and keep their operations running smoothly. The key characteristic of reduced downtime lies in its ability to minimize the impact of unexpected breakdowns, enabling continuous workflow and maximizing productivity. Embracing reduced downtime as a priority choice for this article emphasizes its paramount importance in achieving sustainable operational efficiency.
Improved Resource Utilization
Enhanced resource utilization plays a crucial role in optimizing operational efficiency. By efficiently allocating resources based on maintenance data stored in the database, organizations can prevent underutilization or overutilization of equipment. The defining characteristic of improved resource utilization is its ability to ensure that resources are utilized optimally, thereby enhancing productivity and reducing wastage. Highlighting improved resource utilization as a preferred choice in this article underscores its significance in achieving peak operational performance.
Streamlined Maintenance Processes
Streamlining maintenance processes is essential for promoting efficiency in equipment management. By structuring maintenance tasks and schedules within the database, organizations can create a systematic approach to handling maintenance activities. The key characteristic of streamlined maintenance processes lies in their ability to simplify complex maintenance workflows, thereby reducing errors and enhancing overall effectiveness. Emphasizing streamlined maintenance processes as a strategic choice in this article underscores their role in fostering efficient equipment maintenance and operational success.
Cost Savings and Extended Equipment Lifespan
Optimized Repair and Replacement Costs
Optimizing repair and replacement costs is instrumental in achieving cost savings and maximizing equipment lifespan. By effectively managing repair and replacement cycles through data-driven insights provided by the database, organizations can reduce unnecessary expenditures and prolong the longevity of their equipment. The key characteristic of optimized repair and replacement costs is their potential to optimize operational budgets while ensuring that equipment remains in optimal working condition. Prioritizing optimized repair and replacement costs in this article highlights their contribution to sustainable cost management and prolonged equipment durability.
Prolonged Equipment Durability
Prolonging equipment durability is a key objective in maintaining a well-organized maintenance database. By implementing proactive maintenance strategies based on equipment data stored in the database, organizations can extend the lifespan of their assets and minimize the frequency of replacements. The defining feature of prolonged equipment durability lies in its ability to enhance the resilience of equipment against wear and tear, ultimately reducing lifecycle costs and fostering long-term sustainability. Showcasing prolonged equipment durability as an essential focus in this article underscores its role in preserving asset value and optimizing operational efficiency.
Minimized Emergency Repairs
Minimizing emergency repairs is essential for preventing unplanned disruptions and mitigating potential risks to equipment functionality. By leveraging data analysis and predictive maintenance alerts within the database, organizations can identify early signs of equipment degradation and take preemptive action to avert costly emergency repairs. The unique feature of minimized emergency repairs is its capacity to proactively address maintenance issues, reducing downtime and maintenance costs. Highlighting minimized emergency repairs as a critical consideration in this article underscores its significance in ensuring operational continuity and maximizing equipment reliability.