Unlocking Efficiency: Strategies for Optimizing Building Maintenance Work Orders

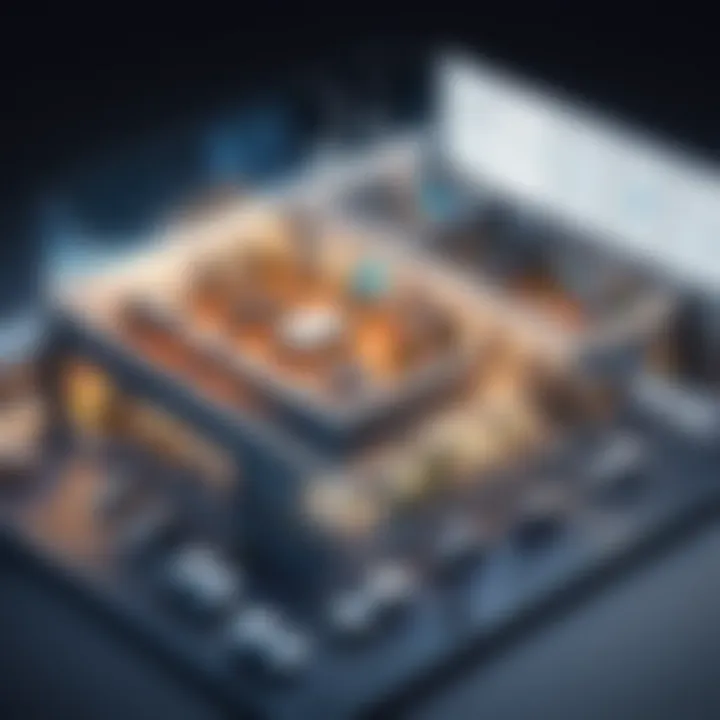
Software Overview and Benefits
As businesses strive for efficiency and streamlined operations, optimizing building maintenance work orders is paramount. One key aspect of this optimization process is leveraging software to enhance workflow management. Introducing a robust maintenance management software can revolutionize how maintenance tasks are assigned, tracked, and completed, ultimately driving overall productivity. This software usually comes equipped with features like work order tracking, asset management, and preventive maintenance scheduling. By centralizing all maintenance activities in one platform, the software simplifies work order management, ensures timely repairs, and increases the longevity of building assets.
Pricing and Plans
When considering the adoption of maintenance management software, evaluating the pricing structure and available subscription plans is crucial. The cost of the software can vary based on factors such as the number of users, the scope of features included, and the level of customization required. It is essential to compare the pricing of different software options in the market to ensure that the chosen solution provides optimal value for the investment. Some software providers offer tiered pricing plans based on company size or specific needs, while others may follow a pay-per-user model. Understanding the pricing landscape can aid in selecting a cost-effective solution that aligns with the organization's maintenance budget.
Performance and User Experience
The performance and user experience of maintenance management software significantly impact its effectiveness in streamlining work order processes. A well-designed software solution should exhibit fast loading times, high system reliability, and an intuitive user interface for seamless navigation. Users should find the software easy to learn and use, minimizing training requirements and accelerating adoption rates across maintenance teams. Feedback from existing users can offer valuable insights into the software's performance, highlighting strengths and areas for improvement. Prioritizing software with superior performance and user experience can contribute to enhanced operational efficiency and increased user satisfaction.
Integrations and Compatibility
In today's interconnected digital landscape, the compatibility and integrations offered by maintenance management software play a pivotal role in ensuring smooth operations. A software solution that integrates seamlessly with other tools and platforms, such as enterprise resource planning (ERP) systems or Internet of Things (IoT) devices, facilitates data sharing and communication between different departments. Additionally, compatibility with various operating systems and devices enables flexibility and accessibility for maintenance teams working across diverse environments. Evaluating the integration capabilities and compatibility of maintenance management software is essential for maximizing its utility within the organization's existing technological ecosystem.
Support and Resources
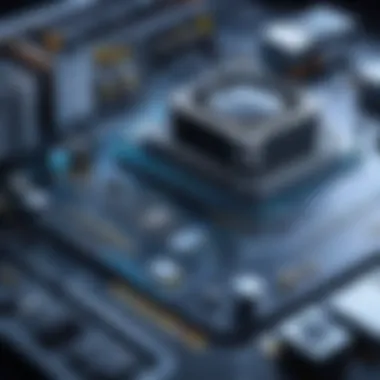
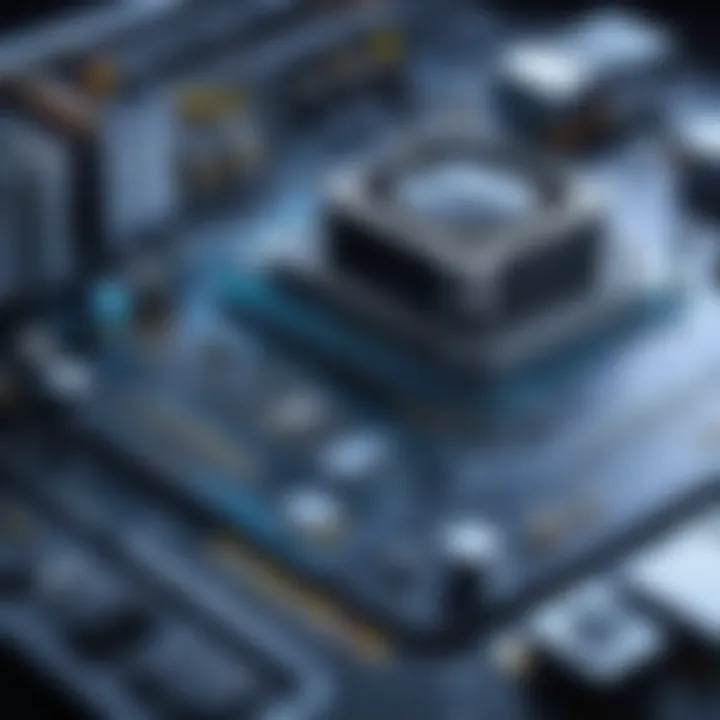
Efficient customer support and access to resources are fundamental elements of a successful software deployment. When selecting maintenance management software, examining the available customer support options is vital for resolving technical issues promptly and ensuring uninterrupted workflow. Whether through phone support, email correspondence, or live chat services, responsive customer support can resolve queries and provide guidance as needed. Furthermore, the availability of resources such as tutorials, guides, and training materials empowers users to leverage the software's full potential, expanding their proficiency and driving operational excellence. Investing in software with reliable support infrastructure and ample resources can optimize the user experience and maximize the benefits gained from adopting maintenance management software.
Prelims to Building Maintenance Work Orders
In the realm of facility management, building maintenance work orders play a pivotal role in ensuring the seamless operation and upkeep of commercial and residential properties. These work orders encapsulate the essential tasks needed for maintenance, repairs, and upkeep activities to be effectively carried out. By instituting a robust work order system, facilities are empowered to address issues proactively, thus preventing the escalation of minor concerns into significant problems that could disrupt operations and incur substantial costs. Understanding the nuances of building maintenance work orders equips facility managers and maintenance teams with the foresight and structure necessary to maintain properties at optimal levels of functionality and aesthetics.
The Significance of Maintenance Work Orders
Maintenance work orders are the lifeblood of effective property management, serving as the bedrock on which maintenance activities are executed. The significance of maintenance work orders lies in their ability to provide a systematic approach to tackling maintenance needs promptly and efficiently. By delineating tasks clearly, assigning responsibilities, and setting timelines, work orders ensure that maintenance activities are conducted in a coordinated manner, reducing downtime and enhancing operational efficiency. Moreover, maintenance work orders facilitate the tracking of maintenance history, enabling insights into recurring issues, areas requiring frequent attention, and the overall health of the property.
Challenges Faced in Managing Work Orders
Despite their essential role, managing work orders presents a distinct set of challenges for facility managers and maintenance teams. One prevalent challenge is the prioritization of work orders, especially in high-traffic or critical areas where maintenance needs are competing for attention. Additionally, the accurate allocation of resources, scheduling maintenance tasks efficiently, and ensuring timely completion of work orders are ongoing challenges that require adept management and streamlined processes. Furthermore, the manual nature of traditional work order systems can lead to inefficiencies, miscommunication, and a lack of transparency, impeding the seamless execution of maintenance activities.
Impact of Inefficient Work Order Processes
Inefficient work order processes can have far-reaching implications on property maintenance, affecting operational efficiency, tenant satisfaction, and cost management. When maintenance tasks are not addressed promptly or systematically, minor issues can snowball into major problems, causing disruptions, safety hazards, and unwarranted expenses. The lack of a structured approach to work order management can result in disorganization, missed deadlines, and inadequate resource utilization, ultimately compromising the upkeep of buildings and diminishing their value. By highlighting the consequences of inefficient work order processes, stakeholders are compelled to reevaluate their strategies and embrace more efficient and technology-driven approaches to maintenance management.
Best Practices for Efficient Work Order Management
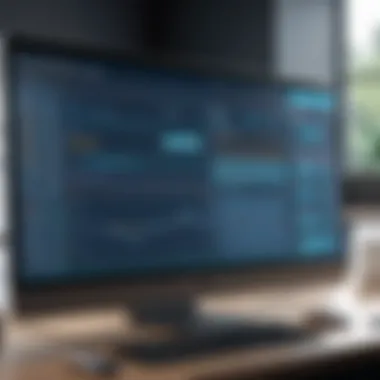
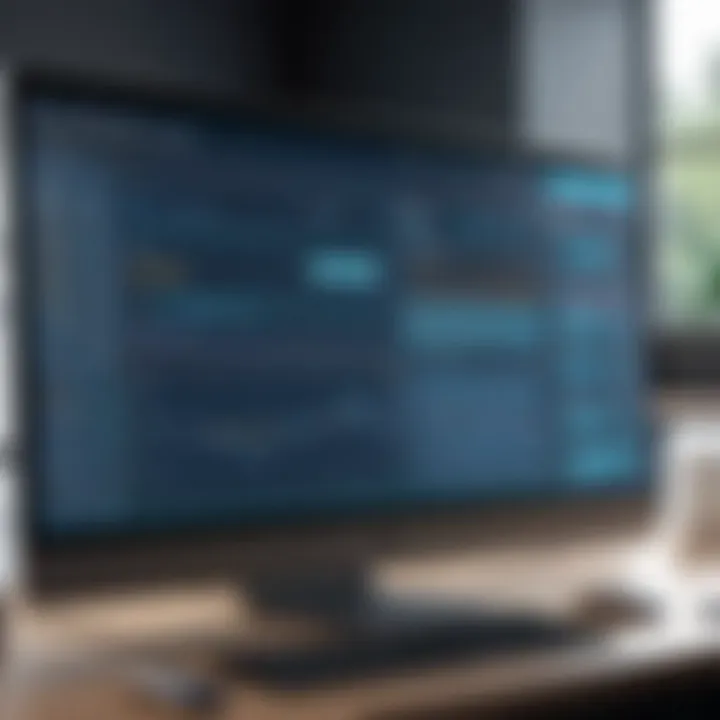
Efficient work order management is a key aspect of maintaining buildings effectively. In this article, we delve into the significance of incorporating best practices to streamline maintenance operations. By implementing efficient work order management practices, facilities can ensure smoother workflows, timely repairs, and enhanced productivity. Prioritizing Maintenance Tasks Prioritizing maintenance tasks is crucial for optimal building upkeep. By categorizing tasks based on urgency, impact on operations, and safety considerations, facilities can allocate resources efficiently. Preventive Maintenance Strategies Utilizing preventive maintenance strategies is essential for reducing unexpected breakdowns and prolonging asset lifespan. Implementing routine inspections, timely servicing, and predictive maintenance measures can prevent costly repairs and enhance equipment performance. Implementing Digital Work Order Systems The integration of digital work order systems revolutionizes maintenance processes. By digitizing work orders, facilities can streamline request submissions, approvals, scheduling, and tracking. This automated approach enhances transparency, reduces manual errors, and improves response times. Optimizing Communication Channels Efficient communication channels are vital for seamless work order management. Clear channels for reporting issues, tracking progress, and sharing updates enhance collaboration between maintenance teams, technicians, and stakeholders. Utilizing digital platforms for real-time notifications and feedback loops can facilitate quick resolutions and improve overall operational efficiency.
Enhancing Efficiency Through Technology
In this section, we delve into the pivotal role of technology in optimizing building maintenance work orders for enhanced efficiency. Technology serves as a catalyst for streamlining processes, improving productivity, and ultimately driving cost-effectiveness in facility management. By embracing cutting-edge digital solutions, facilities managers and maintenance teams can revolutionize their approach to maintenance workflows.
Benefits of Automated Work Order Systems
Automated work order systems stand out as a cornerstone of efficient maintenance management. These systems automate the creation, assignment, and tracking of work orders, reducing manual intervention and minimizing the risk of errors. By leveraging automated systems, organizations can ensure swift response times to maintenance requests, prioritize tasks effectively, and maintain a comprehensive digital record of all maintenance activities.
Integration with IoT for Predictive Maintenance
The integration of Internet of Things (IoT) technologies holds immense promise for predictive maintenance in facility management. By connecting devices, sensors, and equipment to a centralized system, maintenance teams can monitor real-time data to anticipate potential issues before they escalate. This proactive approach enables predictive maintenance, reducing downtime, extending asset lifespan, and optimizing resource utilization.
Utilizing Data Analytics for Decision-Making
Data analytics emerges as a game-changer in facilitating data-driven decision-making for maintenance operations. By harnessing the power of data analytics tools, organizations can derive actionable insights from vast amounts of maintenance data. This enables predictive maintenance scheduling, trend analysis, and resource allocation optimization, empowering maintenance teams to make well-informed decisions that drive operational efficiency and cost savings.
Measuring Success and Improving Processes
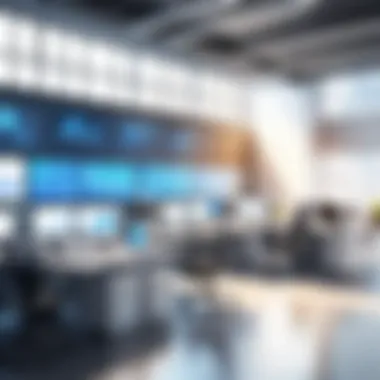
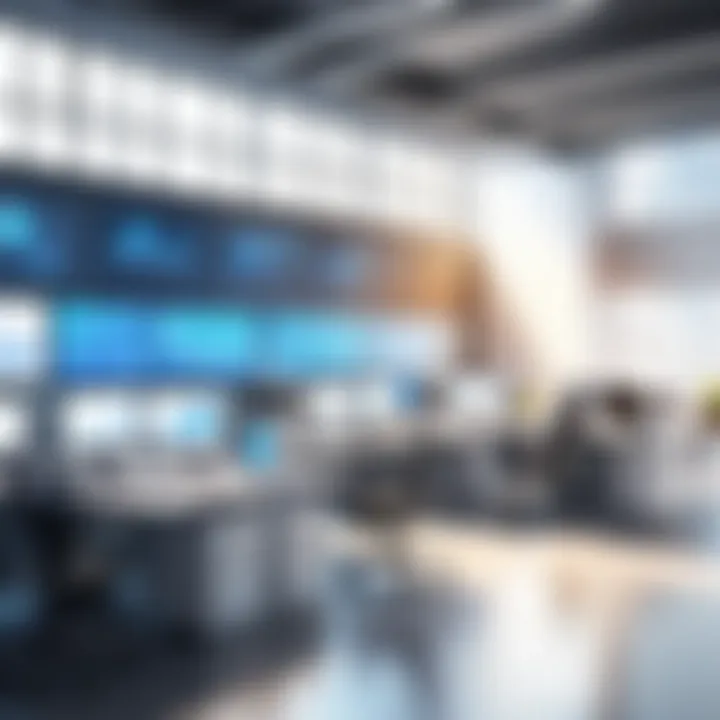
In the realm of building maintenance work orders, the measurement of success and continuous process improvement stand as pivotal pillars in ensuring operational efficiency and optimal performance. Here, the essence lies in meticulously monitoring and assessing various key performance indicators (KPIs) that serve as quantifiable metrics for evaluating work order management effectiveness. By keenly focusing on KPIs, facilities managers and maintenance teams can gauge the health of their maintenance processes, identify areas for enhancement, and make data-driven decisions to uplift overall productivity. These KPIs encompass a wide array of parameters, including but not limited to response times, completion rates, asset downtime, and costs incurred. Through the astute analysis of these indicators, organizations can gain valuable insights into the efficacy of their maintenance workflows, enabling them to pinpoint inefficiencies, address bottlenecks, and refine strategies for enhanced operational excellence.
Key Performance Indicators for Work Order Management
The sphere of work order management brims with a plethora of key performance indicators (KPIs) that serve as guiding beacons for evaluating and optimizing maintenance processes. These KPIs unveil crucial insights into the efficiency, timeliness, and cost-effectiveness of maintenance operations, empowering decision-makers to steer their strategies towards maximum efficacy. Among the fundamental KPIs in work order management are response time metrics, which delineate the speed at which maintenance requests are addressed, reflecting the agility and responsiveness of the maintenance team. Furthermore, asset uptime metrics play a pivotal role in measuring asset reliability and performance, shedding light on the effectiveness of maintenance efforts in minimizing downtime and maximizing operational continuity. By delving deep into these KPIs and leveraging data analytics tools, organizations can not only track performance trends but also proactively identify areas for improvement, fostering a culture of continuous enhancement and optimization in their maintenance processes.
Continuous Evaluation and Feedback Mechanisms
Continuous evaluation and feedback mechanisms serve as indispensable conduits for cultivating a culture of incessant improvement and refinement in building maintenance work orders. Through the regular assessment of maintenance workflows, team performance, and customer satisfaction levels, organizations can proactively identify pain points, rectify inefficiencies, and enhance service delivery standards. By soliciting feedback from stakeholders, including residents, tenants, and in-house teams, organizations can gain invaluable perspectives on the efficacy of their maintenance operations, pinpoint areas for enhancement, and tailor their approaches to better cater to user needs and preferences. This iterative feedback loop not only fosters greater transparency and accountability but also cultivates a customer-centric ethos within maintenance teams, driving them towards higher standards of service excellence, satisfaction, and operational efficiency.
Iterative Improvements in Maintenance Workflows
Iterative improvements in maintenance workflows form the cornerstone of operational excellence in building maintenance work orders, embodying a cyclical process of enhancement, refinement, and innovation. By embracing a culture of continual learning and adaptation, maintenance teams can systematically evaluate their processes, identify areas for optimization, and implement incremental changes to elevate efficiency and effectiveness. Through a structured approach of analyzing performance data, soliciting feedback, and fostering cross-departmental collaboration, organizations can drive iterative improvements that result in streamlined workflows, enhanced service quality, and cost savings. Moreover, by leveraging emerging technologies, such as predictive maintenance solutions and workflow automation tools, maintenance teams can further expedite their evolution towards proactive maintenance strategies, predictive insights, and agile operational frameworks. This iterative journey of improvement not only bolsters organizational resilience and responsiveness but also ensures that maintenance processes remain agile, adaptive, and aligned with evolving industry standards and best practices.
Epilogue
In this article, the focus has been on honing the efficiency of building maintenance work orders, crucial for seamless operations in facilities management. The Conclusion section encapsulates the essence of the discourse, emphasizing the significance of implementing strategies for optimized work order management. By synthesizing the strategies discussed throughout this article, a holistic view emerges, underlining the pivotal role efficient work order processes play in maximizing productivity and ensuring the longevity of building assets.
Summarizing Strategies for Efficient Work Order Management
Efficient work order management hinges on a robust framework encompassing prioritization, preventive maintenance, digital solutions, and streamlined communication channels. Prioritizing maintenance tasks based on criticality and impact is fundamental for resource allocation and timely resolutions. Leveraging preventive maintenance strategies forestalls costly breakdowns, prolonging equipment lifespan and avoiding disruptions. Integrating digital work order systems automates workflows, enhancing visibility and accountability. Optimizing communication channels fosters collaboration and expedites problem-solving, ensuring seamless operations.
Embracing Innovation in Building Maintenance Practices
Embracing innovation in building maintenance practices is imperative for staying ahead in a dynamic landscape. Incorporating cutting-edge technologies like IoT for predictive maintenance revolutionizes traditional approaches, shifting maintenance from reactive to proactive. The benefits of harnessing data analytics for decision-making are immense, empowering facilities managers to make informed choices backed by insights. By embracing innovation, organizations future-proof their maintenance operations, increasing efficiency, reducing costs, and enhancing overall performance.