Unveiling the Profound Influence of QAD Manufacturing on Modern Industry Dynamics

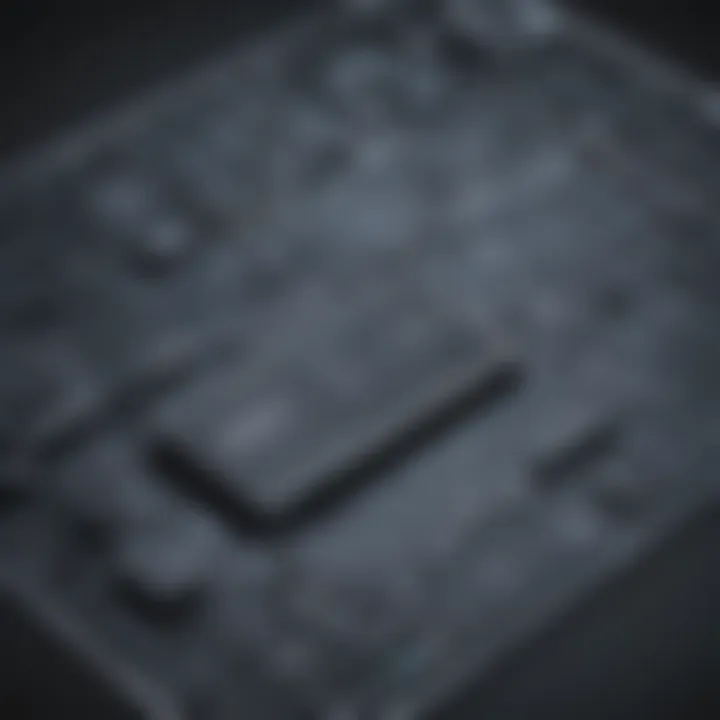
Software Overview and Benefits
- In the domain of modern industry operations, the role of QAD manufacturing software is substantial in optimizing production processes and bolstering quality control measures. This software intricately meshes with organizational workflows to enhance operational efficiencies, thereby propelling businesses towards success. Leverage the key features of QAD manufacturing software to streamline your operations and ensure a competitive edge in the market.
Pricing and Plans
- When considering the implementation of QAD manufacturing software, exploring the pricing structures and available subscription plans is imperative. By dissecting the pricing details and comparing them with competitors in the same category, businesses can invest judiciously in a software solution that aligns with their unique needs and budgetary constraints.
Performance and User Experience
- The evaluation of a software's performance is crucial in determining its efficacy in driving organizational outcomes. Assess the speed, reliability, and user interface of QAD manufacturing software to ascertain its compatibility with your operational requirements. Additionally, gather insights from user experiences to glean valuable feedback on usability, ensuring a seamless integration into your existing workflows.
Integrations and Compatibility
- Explore the integrations offered by QAD manufacturing software with other tools and platforms to ascertain its versatility and suitability within your business ecosystem. By delving into the compatibility of the software with various operating systems and devices, you can seamlessly integrate QAD manufacturing into your technological infrastructure, enhancing connectivity and workflow efficiency.
Support and Resources
- Access to comprehensive customer support options is essential for leveraging the full potential of QAD manufacturing software. Navigate the array of support resources, including tutorials, guides, and training materials, to empower users with the knowledge and skills required to optimize their software utilization. By harnessing these resources, businesses can maximize the benefits of QAD manufacturing software and drive innovation within their operational frameworks.
Introduction to QAD Manufacturing
QAD Manufacturing stands at the forefront of modern industry dynamics, revolutionizing operational efficiencies and driving business success to unparalleled heights. From optimizing production processes to enhancing quality control measures, the emergence of QAD Manufacturing has become a disruptive force in the industrial landscape. This section delves deep into the core concepts of QAD Manufacturing, shedding light on its significance in the realm of contemporary manufacturing methodologies.
Understanding QAD Manufacturing Principles
The Evolution of QAD Practices
The Evolution of QAD Practices signifies a pivotal shift in manufacturing ideologies, marking a transition towards more agile and adaptive production frameworks. Embracing technological advancements and business innovations, The Evolution of QAD Practices has engraved its prominence by aligning manufacturing processes with the demands of the digital era. Its emphasis on real-time data integration and predictive analytics has propelled organizations towards proactive decision-making, redefining standards of operational excellence and market competitiveness within the industry. The distinctive nature of The Evolution of QAD Practices lies in its ability to streamline operations, optimize supply chains, and foster a culture of continual improvement, thus cementing its status as a pioneering approach towards sustainable manufacturing practices in the contemporary setting.
Key Concepts and Components
Key Concepts and Components underpin the foundation of QAD Manufacturing, encapsulating fundamental principles essential for orchestrating seamless production workflows. As the cornerstone of manufacturing efficiency, Key Concepts and Components elucidates the core elements that drive productivity and quality within manufacturing environments. Its versatility lies in its adaptability across diverse industries, making it a universal choice for organizations seeking to enhance their manufacturing capabilities. By integrating cutting-edge technologies and best practices, Key Concepts and Components foster innovation, reliability, and resilience in manufacturing operations. While presenting a myriad of advantages, Key Concepts and Components may pose challenges related to initial implementation costs and organizational change management strategies, warranting meticulous planning and strategic foresight for optimal outcomes.
Benefits of Implementing QAD Manufacturing
Enhanced Production Efficiency
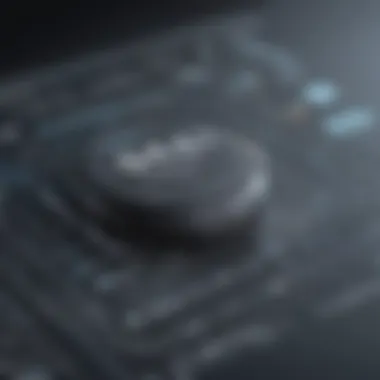
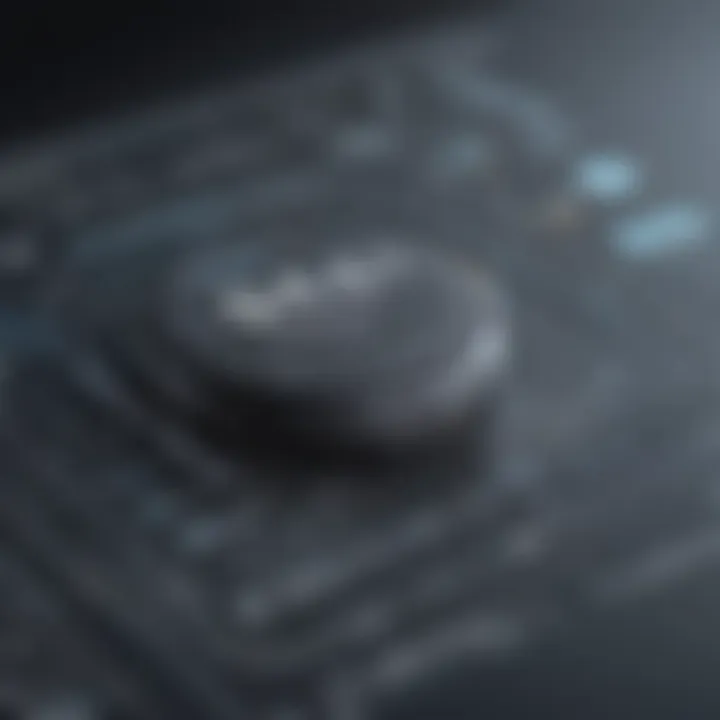
Enhanced Production Efficiency unleashes a new era of manufacturing prowess, redefining traditional paradigms to maximize output and minimize bottlenecks. By leveraging data-driven insights and automated workflows, Enhanced Production Efficiency optimizes resource utilization, accelerates time-to-market, and fosters a culture of operational agility. Its intrinsic value lies in
Integration of QAD Manufacturing Systems
QAD Manufacturing Systems integration is a critical aspect of modern industrial operations, revolutionizing the way businesses manage their production processes. By seamlessly incorporating QAD solutions into existing systems, organizations can achieve enhanced operational efficiency and streamlined workflows. The integration of QAD Manufacturing Systems encompasses various components such as Enterprise Resource Planning (ERP) and Supply Chain Management, which play pivotal roles in optimizing manufacturing processes.
Streamlining Operations with QAD Solutions
ERP Integration
ERP Integration within the context of QAD Manufacturing Systems is a fundamental element that centralizes data and streamlines business processes. By integrating ERP systems with QAD solutions, organizations can synchronize their operations, eliminate redundancies, and improve data accuracy. The key characteristic of ERP Integration lies in its ability to create a unified platform for managing resources, enhancing decision-making processes, and boosting overall efficiency. This integration offers real-time insights, facilitates better resource allocation, and promotes seamless communication across departments. However, challenges such as initial setup costs and system compatibility issues can pose obstacles to seamless integration. Organizations need to carefully assess their requirements and choose ERP Integration strategies that align with their long-term goals to reap maximum benefits.
Supply Chain Management
In the realm of QAD Manufacturing Systems, Supply Chain Management stands out as a crucial component that influences operational success. Effective Supply Chain Management within QAD solutions ensures timely production, minimizes delays, and enhances customer satisfaction. The key characteristic of Supply Chain Management lies in its ability to optimize inventory levels, streamline procurement processes, and foster collaboration between suppliers and manufacturers. Businesses adopting Supply Chain Management solutions witness improved visibility into their supply chain, reduced lead times, and increased responsiveness to market demands. While the unique feature of Supply Chain Management lies in its ability to mitigate risks and enhance supply chain resilience, challenges such as supply chain disruptions and fluctuating market conditions require proactive strategies to maintain efficiency. Organizations must leverage advanced supply chain tools offered by QAD Manufacturing Systems to mitigate risks, optimize inventory costs, and ensure seamless supply chain operations.
Optimizing Quality Control with QAD
In this section, we delve into the crucial topic of Optimizing Quality Control with QAD manufacturing in modern industry. Quality control is a cornerstone of manufacturing processes, ensuring products meet stringent standards and customer expectations. Implementing robust quality control measures through QAD technologies can vastly enhance operational efficiencies and streamline production workflows. By integrating quality control protocols within the QAD framework, organizations can achieve unparalleled accuracy and consistency in their output. This optimization not only bolsters product quality but also minimizes errors, ultimately leading to greater customer satisfaction and loyalty.
Implementing Quality Assurance Measures
ISO Standards Compliance
ISO Standards Compliance stands as a pinnacle of regulatory adherence in manufacturing practices. Complying with ISO standards signifies a commitment to quality, safety, and efficiency. By adopting ISO Standards Compliance within QAD manufacturing systems, companies exhibit a proactive approach towards meeting global benchmarks for product excellence. The structured framework of ISO standards instills a disciplined quality culture within organizations, fostering continuous improvement and stakeholder confidence. While adhering to ISO requirements can involve meticulous documentation and process adjustments, the long-term benefits in terms of market competitiveness and operational resilience make it a worthy investment for businesses embracing QAD methodologies.
Continuous Improvement Initiatives
Continuous Improvement Initiatives underpin a culture of perpetual enhancement within manufacturing setups. By emphasizing Kaizen philosophies and process refinement, organizations can elevate their productivity and quality benchmarks. Implementing Continuous Improvement Initiatives alongside QAD manufacturing empowers teams to identify inefficiencies, rectify errors promptly, and drive iterative progress. The structured approach of continuous improvement ensures that operations remain agile and responsive to evolving market demands. While integrating these initiatives may require a shift in organizational mindset and resource allocation, the benefits of sustained growth, cost savings, and enhanced customer value underscore its significance within the QAD manufacturing landscape.
Real-Time Monitoring and Reporting
In the realm of manufacturing, Real-Time Monitoring and Reporting play a pivotal role in quality assurance and performance optimization. By employing advanced quality metrics analysis tools, companies can gain real-time insights into production processes and identify deviations swiftly. Quality Metrics Analysis allows for proactive decision-making, enabling preemptive quality control interventions and ensuring compliance with set standards. Through sophisticated defect tracking systems, organizations can trace and rectify quality issues promptly, preventing recurrence and preserving brand reputation. The integration of Real-Time Monitoring and Reporting mechanisms with QAD manufacturing paves the way for data-driven decision-making, operational transparency, and continuous quality enhancement.
The Role of QAD Manufacturing in Lean Practices
QAD Manufacturing in Lean Practices focuses on optimizing operational efficiency within businesses by implementing lean principles. This section dives deep into how Lean Practices impact modern industry dynamics, offering a detailed examination of the specific elements and benefits associated with integrating QAD into lean methodologies. Highlighting the importance of waste reduction strategies and Kaizen methodologies, this aspect of the article sheds light on how QAD manufacturing enhances organizational agility and productivity.
Implementing Lean Manufacturing Principles
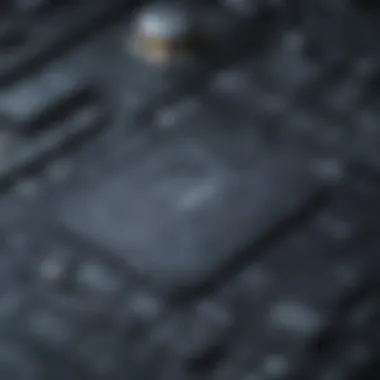
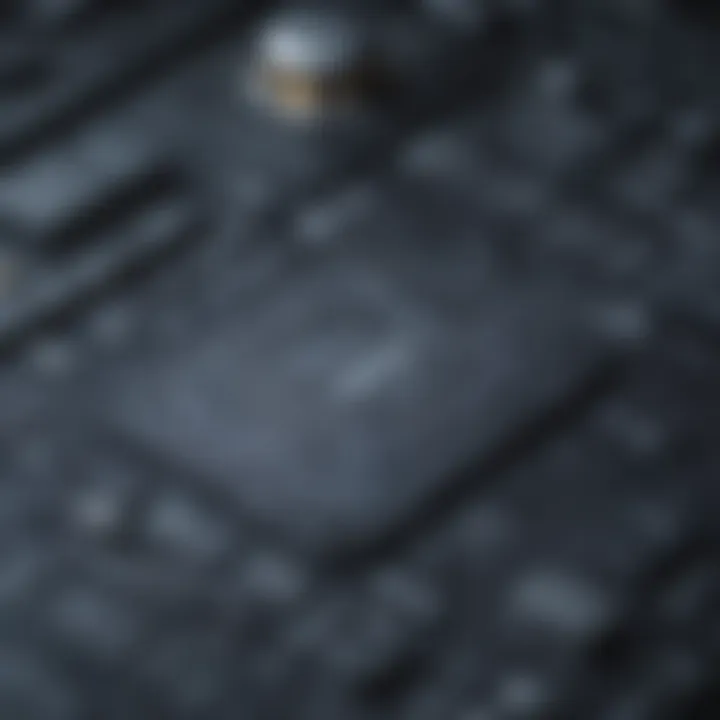
Waste Reduction Strategies
Waste Reduction Strategies play a crucial role in minimizing inefficiencies and maximizing resource utilization in manufacturing processes. Within the context of this article, Waste Reduction Strategies are highlighted as key tools for streamlining operations and enhancing overall production efficiency. The unique feature of these strategies lies in their ability to identify and eliminate non-value adding activities, ultimately leading to cost savings and operational improvements. Understanding the advantages and disadvantages of Waste Reduction Strategies is fundamental in grasping their significance in the optimization of manufacturing operations.
Kaizen Methodologies
Kaizen Methodologies form the foundation of continuous improvement within manufacturing environments by encouraging incremental enhancements to processes and systems. In the realm of QAD manufacturing, Kaizen Methodologies are instrumental in driving operational excellence and fostering a culture of innovation. This section elaborates on the key characteristics of Kaizen, emphasizing its iterative approach to problem-solving and its ability to cultivate a mindset of continuous learning and development. Exploring the advantages and potential drawbacks of Kaizen Methodologies provides readers with valuable insights into their application and impact on operational efficiency.
Achieving Operational Excellence through QAD
In the pursuit of operational excellence, businesses leverage QAD Manufacturing to streamline processes and enhance productivity. This section delves into the role of Continuous Flow Processes and Poka-Yoke Techniques in optimizing workflows and ensuring consistent quality standards.
Continuous Flow Processes
Continuous Flow Processes orchestrate a seamless flow of activities within manufacturing operations, eliminating bottlenecks and optimizing resource allocation. Within the scope of this article, Continuous Flow Processes are portrayed as essential components of lean methodologies, enabling organizations to achieve high levels of efficiency and output consistency. The distinctive feature of Continuous Flow lies in its ability to synchronize tasks and minimize idle time, leading to enhanced productivity and reduced lead times. Delving into the advantages and potential drawbacks of Continuous Flow Processes offers readers a comprehensive understanding of their impact on operational efficiency.
Poka-Yoke Techniques
Poka-Yoke Techniques focus on error-proofing processes to prevent mistakes and defects from occurring during production. As an integral part of QAD Manufacturing practices, Poka-Yoke plays a vital role in enhancing product quality and reducing rework instances. This segment elucidates the key characteristics of Poka-Yoke, emphasizing its role in ensuring first-time-right production and enhancing overall production reliability. Exploring the advantages and disadvantages of Poka-Yoke Techniques provides readers with valuable insights into their contribution to operational excellence.
Embracing Industry with QAD Innovations
In modern industry, the integration of Industry 4.0 concepts with QAD innovations is paramount for achieving operational excellence and staying ahead in a competitive landscape. Industry 4.0 represents the new wave of digital transformation in manufacturing, emphasizing automation, data exchange, IoT, cloud computing, and other technologies to create 'smart factories.' QAD innovations play a crucial role in harnessing the potential of Industry 4.0 by enabling seamless connectivity, real-time data insights, and predictive analytics.
Harnessing IoT in Manufacturing
Smart Factory Applications
Smart Factory Applications are a cornerstone of Industry 4.0, revolutionizing manufacturing processes through IoT connectivity and intelligent automation. These applications leverage IoT sensors, devices, and platforms to monitor, control, and optimize various production stages in real-time. The key characteristic of Smart Factory Applications lies in their ability to facilitate data-driven decision-making, enhance productivity, and adapt swiftly to changing market demands. Their unique feature of enabling interconnectivity across machines, systems, and humans ensures a responsive and agile manufacturing environment. Despite the advantages of improved efficiency and flexibility, challenges such as cybersecurity risks and high implementation costs need careful consideration in integrating Smart Factory Applications within QAD frameworks.
Predictive Maintenance Systems
Predictive Maintenance Systems are instrumental in preemptively identifying equipment failures or performance degradation using advanced data analytics and machine learning algorithms. By analyzing historical data, these systems forecast maintenance needs, schedule proactive repairs, and optimize operational uptime. The key characteristic of Predictive Maintenance Systems is their ability to reduce downtime, lower maintenance costs, and enhance overall equipment effectiveness. Their unique feature in enabling condition-based monitoring and predictive analytics offers a proactive approach to maintenance, preventing costly breakdowns and improving asset reliability. While advantageous in increasing machinery longevity and efficiency, challenges such as data accuracy and integration complexities must be addressed when adopting Predictive Maintenance Systems in conjunction with QAD solutions.
Adopting AI and Robotics in Production
Machine Learning Integration
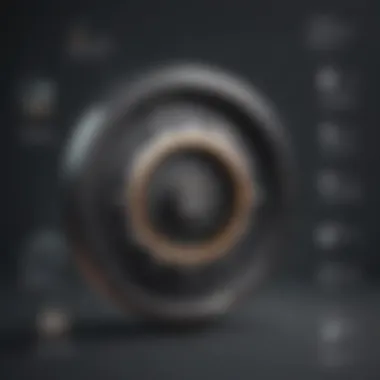
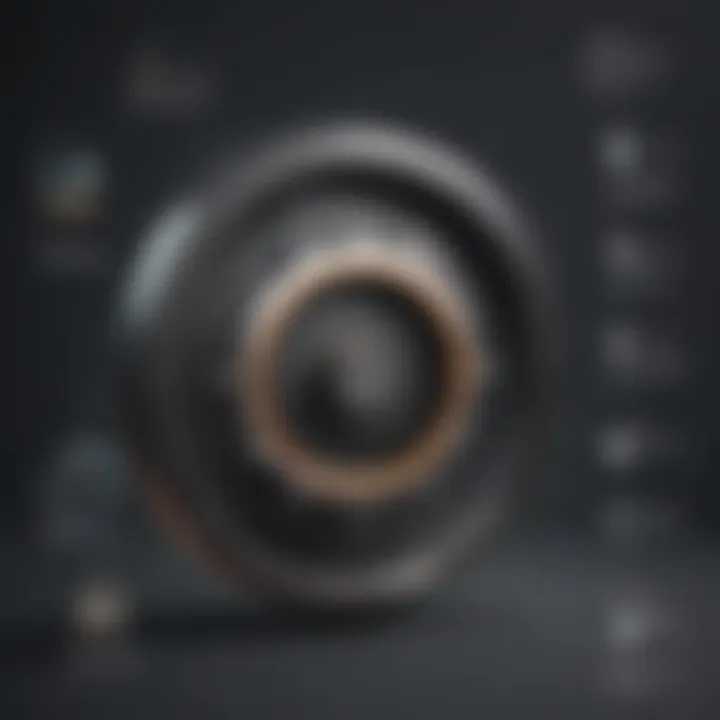
Machine Learning Integration empowers manufacturing processes with predictive insights, pattern recognition, and cognitive automation capabilities. By training algorithms on historical data, Machine Learning Integration predicts outcomes, optimizes production workflows, and automates decision-making tasks. The key characteristic of Machine Learning Integration is its capacity to continuously learn and improve based on new information, enhancing process efficiency and quality control. Its unique feature in identifying patterns, anomalies, and optimization opportunities drives ongoing operational enhancements. While advantageous in boosting production accuracy and innovation, challenges related to data privacy and regulatory compliance require cautious management when integrating Machine Learning with QAD manufacturing solutions.
Automated Assembly Technologies
Automated Assembly Technologies revolutionize the production line through robotic automation, precision engineering, and workflow optimization. These technologies utilize robots, conveyors, and sensors to streamline assembly tasks, reduce manual labour, and increase output speeds. The key characteristic of Automated Assembly Technologies lies in their ability to achieve consistent quality, high throughput rates, and ergonomic improvements in manufacturing environments. Their unique feature in enabling 247 production capabilities and scalability supports operational efficiency and cost-effectiveness. Despite the advantages of enhanced productivity and reduced human error, challenges such as initial investments and retraining requirements pose considerations for integrating Automated Assembly Technologies within QAD manufacturing setups.
Challenges and Solutions in QAD Implementation
In the realm of manufacturing, the implementation of QAD (Quality Assurance and Determination) systems presents both challenges and solutions crucial for operational success. The efficient integration of QAD practices often faces resistance and obstacles that demand strategic solutions to ensure seamless adoption and realization of benefits. Addressing these challenges head-on is imperative for businesses seeking to enhance their production processes and quality control measures in alignment with modern industry standards.
Overcoming Resistance to Change
Employee Training Programs
Employee training programs constitute a cornerstone in overcoming resistance to change within QAD implementation. These programs focus on equipping staff with the necessary skills and knowledge to adapt to new technology and processes effectively. The comprehensive training initiatives play a pivotal role in fostering a culture of continuous learning and development among employees, ultimately enhancing their capabilities to navigate the evolving landscape of QAD manufacturing. By investing in employee training programs, organizations can cultivate a workforce that is proficient in utilizing QAD systems to their full potential, driving operational efficiencies and quality improvements.
Change Management Strategies
Change management strategies serve as a linchpin in guiding organizational transitions during QAD implementation. These strategies encompass meticulous planning, communication, and stakeholder engagement to mitigate resistance and facilitate smooth adoption of new processes. By delineating clear objectives, responsibilities, and timelines, change management strategies provide a structured framework for navigating changes induced by QAD integration. Moreover, these strategies prioritize proactive problem-solving and feedback mechanisms to address employee concerns and uncertainties, fostering a harmonious transition towards optimized manufacturing practices.
Ensuring Data Security and Compliance
In the digital age, data security and regulatory compliance are paramount considerations in QAD implementation to safeguard sensitive information and uphold industry standards. Ensuring robust cybersecurity measures is essential to fortify manufacturing systems against cyber threats and unauthorized access, mitigating risks of data breaches and operational disruptions. By implementing advanced encryption protocols, access controls, and threat detection mechanisms, organizations can instill confidence in the integrity and confidentiality of their data, bolstering trust among stakeholders.
Cybersecurity Measures
Strategically deploying cybersecurity measures forms a critical defense mechanism against cyber attacks and data breaches in the realm of QAD manufacturing. These measures encompass firewalls, intrusion detection systems, and vulnerability assessments to proactively identify and counteract security threats. By instating a multi-layered security architecture, organizations can augment their resilience to cyber risks, ensuring uninterrupted operations and data integrity within their manufacturing ecosystems.
Regulatory Framework Adherence
Adhering to regulatory frameworks is indispensable for maintaining operational compliance and upholding ethical standards in QAD manufacturing. Compliance with industry regulations and standards not only mitigates legal risks but also instills trust and credibility among stakeholders. By regularly monitoring and aligning with evolving regulatory requirements, organizations can demonstrate a commitment to transparency and accountability, positioning themselves as responsible players in the dynamic landscape of modern manufacturing.
Future Trends and Prospects of QAD Manufacturing
In the ever-evolving landscape of modern industry, anticipating future trends and prospects in QAD manufacturing holds significant importance. Understanding the trajectory of technological advancements and strategic developments is paramount for businesses to stay ahead. Exploring the potential enhancements and challenges that lie ahead is crucial for informed decision-making and sustainable growth. This section delves deep into the emerging trends that will shape the future of QAD manufacturing, providing insights that equip organizations to adapt and thrive in a competitive environment.
Advancements in Smart Manufacturing Technologies
Digital Twins
Digital Twins represent a groundbreaking concept in smart manufacturing technologies. These virtual replicas of physical assets or processes enable real-time monitoring, analysis, and optimization. The crux of Digital Twins lies in their ability to mimic and simulate real-world scenarios, offering a platform for predictive maintenance and performance enhancements. The seamless integration of Digital Twins into manufacturing operations facilitates data-driven decision-making and proactive problem-solving. The intrinsic value of Digital Twins lies in their ability to enhance operational efficiencies, minimize downtime, and optimize resource utilization.
Augmented Reality Applications
Augmented Reality (AR) Applications present a novel approach to revolutionizing manufacturing processes. By overlaying digital information onto the physical world, AR Applications enhance worker productivity, training efficiency, and task accuracy. The key characteristic of AR lies in its ability to superimpose data, instructions, and interactive elements onto the factory floor in real-time, cultivating a more dynamic and intuitive work environment. The unique feature of AR Applications lies in their capacity to bridge the gap between physical and digital realms, fostering enhanced collaboration, error reduction, and operational precision. While the advantages of AR Applications in augmenting design visualization and facilitating remote assistance are clear, challenges such as integration complexities and cost implications require thorough consideration in harnessing their full potential within manufacturing settings.