Unveiling the Crucial Role of Bill of Material in ERP Systems for Enhanced Product Data Management
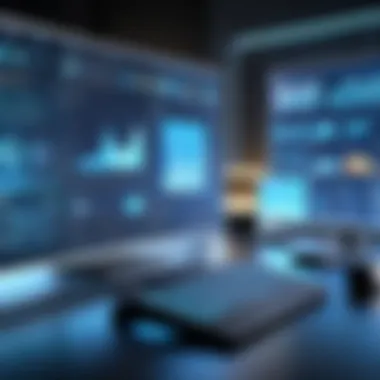
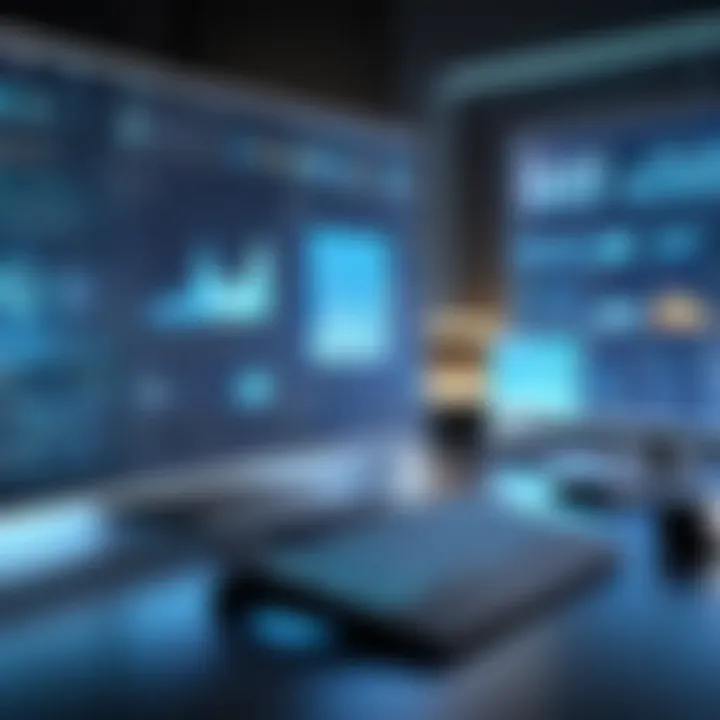
Software Overview and Benefits
In the realm of Enterprise Resource Planning (ERP) systems, the Bill of Material (Bo M) plays a pivotal role in orchestrating the intricate dance of product data management and manufacturing processes. A seamless integration of information, the BoM acts as a blueprint for assembling products and serves as a linchpin for operational success within organizations. Its core function is to elucidate the components, materials, and sub-assemblies required to manufacture a final product, providing comprehensive insights into the entire production lifecycle.
Pricing and Plans
When evaluating the implementation of a robust Bo M within an ERP system, it is crucial to consider the associated costs and pricing structures. These systems vary in pricing, often depending on the scale of the organization and the functionalities required. By comparing the cost of implementing a BoM in different ERP systems, businesses can make informed decisions regarding the economic viability of each option and select a solution that aligns best with their budget and operational needs.
Performance and User Experience
The performance and user experience of an ERP system with integrated Bo M functionality are paramount to the efficiency and effectiveness of manufacturing processes. The speed at which the system processes data, its reliability in delivering accurate information, and the intuitiveness of the user interface all contribute to a seamless operational ecosystem. Through user feedback and in-depth evaluations, businesses can ascertain the optimal ERP system that enhances productivity and fosters a user-friendly environment for all stakeholders.
Integrations and Compatibility
In the contemporary landscape of interconnected technologies, the seamless integration of ERP systems with other tools and platforms is essential for maximizing operational efficiency. A robust Bo M within an ERP system should offer versatile integrations with various software solutions to ensure streamlined processes across different facets of the organization. Additionally, assessing the compatibility of the ERP system and BoM functionality with different operating systems and devices is imperative to guarantee a cohesive digital infrastructure tailored to the specific requirements of the business.
Support and Resources
While the technical capabilities of an ERP system and its integrated Bo M are crucial, the availability of reliable customer support and supplemental resources further enhances the user experience. Comprehensive customer support options, including technical assistance and troubleshooting guidance, empower users to leverage the full potential of the ERP system without disruptions. Moreover, the presence of tutorials, guides, and training materials equips users with the knowledge and skills necessary to navigate the system proficiently and optimize its functionality to suit their organizational objectives.
Introduction to Bill of Material
Bill of Material, commonly referred to as BOM, stands as a crucial element within Enterprise Resource Planning (ERP) systems. This segment of the article delves into the core significance of comprehending BOM within the realm of ERP. Understanding the essence of BOM is paramount as it serves as the foundation for efficient manufacturing processes and streamlined product data management.
Definition and Purpose
Key concept in manufacturing
Key Concept in manufacturing unravels the fundamental building blocks of a product assembly. It encapsulates the comprehensive list of components, sub-assemblies, and raw materials essential for product fabrication. Embracing Key Concept in manufacturing optimizes production processes by offering a detailed breakdown of necessary elements for assembly. Its meticulous nature ensures that every constituent part is accounted for, enhancing manufacturing precision. While its detailed approach aids in precision, it can also make the process lengthy if not streamlined effectively.
Lists components, sub-assemblies, and raw materials
Lists Components, sub-assemblies, and raw materials highlight the granular details required for production processes. By meticulously listing down every component and raw material, this aspect ensures a holistic approach to manufacturing, leaving no room for oversight. Its comprehensive nature enables efficient inventory control and enhances cost estimation accuracy. However, managing an extensive list of components can sometimes introduce complexities, demanding meticulous attention to detail and robust organizational strategies.
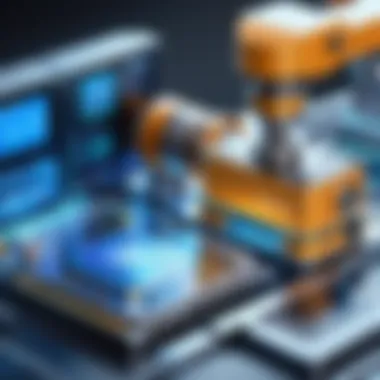
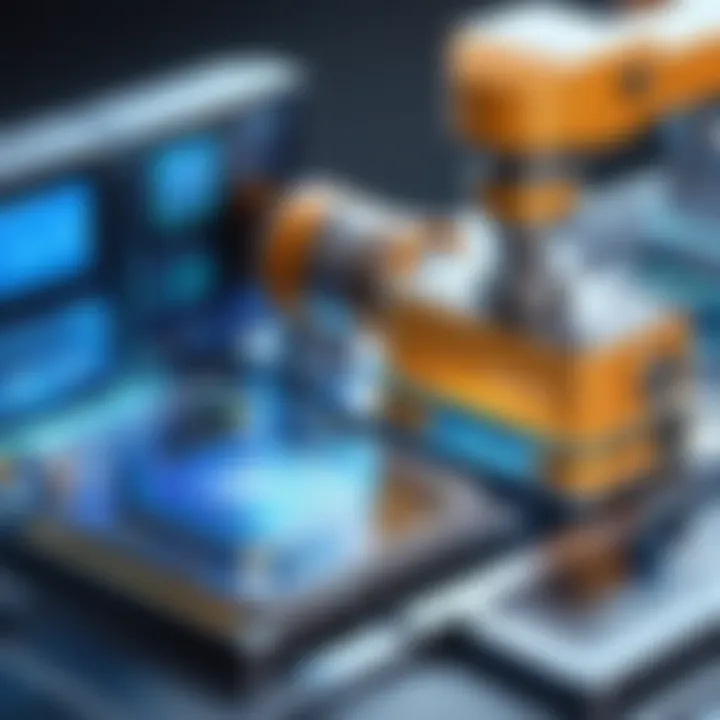
Importance in ERP Systems
Integral for product structure management
Being integral for product structure management, BOM serves as the backbone of product data organization. It ensures that every product is built with precision, maintaining consistency across manufacturing processes. This aspect streamlines product development, facilitating enhanced coordination among different departments involved in the production cycle. While crucial for harmonizing processes, the intricate nature of managing product structures necessitates dedicated attention to detail to prevent errors.
Enables cost estimation and inventory control
Enabling cost estimation and inventory control, BOM plays a pivotal role in financial planning and resource management. By providing a detailed breakdown of components and materials required for each product, it empowers organizations to accurately forecast costs and streamline inventory levels. This streamlined approach enhances operational efficiency and cost-effectiveness. However, the accuracy of cost estimations heavily relies on meticulous data input and consistent updating to reflect market fluctuations accurately.
Components of a Bill of Material
Understanding the significance of Components of a Bill of Material in ERP Systems is crucial for effective product management and manufacturing processes. The components of a Bill of Material play a vital role in detailing the structure of a product, listing all the necessary parts, components, and raw materials required for assembly. By defining the components, a BOM enables accurate cost estimation, streamlined inventory control, and efficient production planning, ensuring smooth operations within an ERP system.
BOM Levels
Single-level BOM
Single-level BOM focuses on listing the components directly used in the assembly of a product without delving into further sub-assemblies. This level of BOM simplifies the structure, making it easier to manage and control. Its straightforward design allows for quick identification of parts and straightforward cost estimation, making it a popular choice for simpler product structures.
Multi-level BOM
Multi-level BOM extends beyond the single level, incorporating sub-assemblies and components within a more complex hierarchical structure. This type of BOM offers a detailed breakdown of materials, enabling a comprehensive understanding of the product structure. While multi-level BOMs provide in-depth insights, they require meticulous management and may pose challenges in terms of complexity and data accuracy.
Indented BOM
Indented BOM showcases the hierarchical relationship between assemblies, sub-assemblies, and individual parts through an indented format. This visually organized layout enhances clarity in understanding how components fit together, aiding in visualizing the product structure effectively. Indented BOMs excel in presenting a clear overview of the manufacturing process but may require meticulous attention to detail for accurate data representation.
BOM Attributes
Part number
The part number serves as a unique identifier for each component within a BOM, facilitating efficient tracking and referencing during production. Its inclusion in the BOM enhances inventory management, streamline ordering processes, and enables quick identification of parts during the assembly process. However, managing numerous part numbers can lead to complexity in data maintenance and consistency.
Quantity per assembly
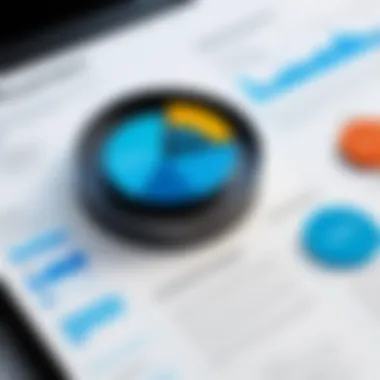
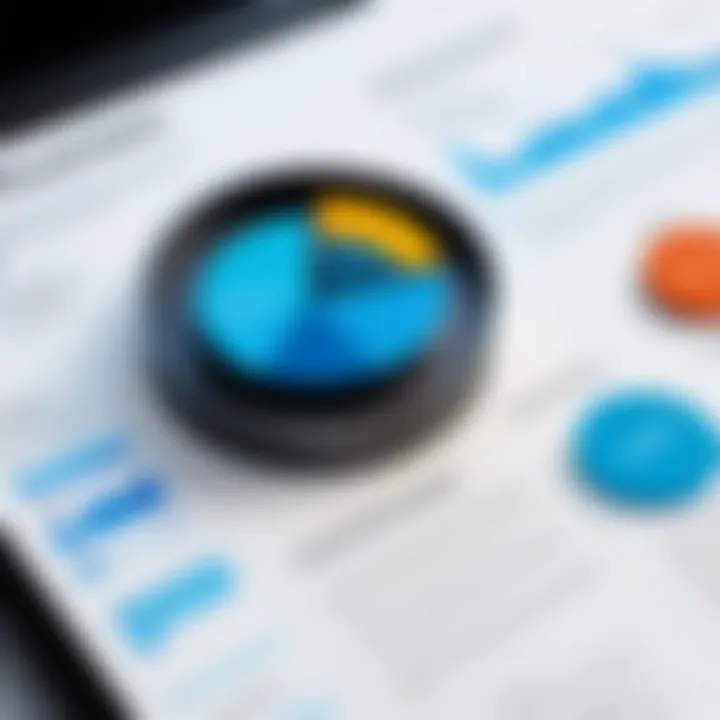
The quantity per assembly specifies the amount of each component required to construct a single unit of the product. By defining quantities accurately, manufacturers can optimize inventory levels, reduce wastage, and ensure smooth production processes. While precise quantities enhance efficiency, inaccurate estimations can result in material shortages or surplus, impacting production timelines.
Reference designators
Reference designators associate specific components with their physical locations on the product design, aiding in assembly and maintenance. By including reference designators in the BOM, manufacturers can streamline the assembly process, reduce errors, and facilitate repairs and replacements efficiently. However, maintaining consistent reference designations across various products may require robust tracking systems and documentation to avoid confusion or errors.
Creating and Managing BOM in ERP
When delving into the complexities of ERP systems, the creation and management of a Bill of Material (BOM) holds a crucial role. In essence, the BOM serves as the cornerstone for product data management within ERP, streamlining the entire manufacturing process. Efficiency in creating and managing BOMs is not just a process but a strategic necessity that impacts various facets of operations. Understanding the intricate details of how BOMs are structured and updated in ERP systems is paramount for optimizing productivity and enhancing decision-making processes.
Data Entry and Validation
Accuracy is key
Analyzing the meticulous process of data entry and validation in ERP systems reveals the critical importance of accuracy. Inaccurate data input can lead to significant ramifications throughout the manufacturing chain, impacting production timelines, resource allocation, and ultimately, customer satisfaction. Ensuring precise data entry demands attention to detail and a commitment to error-free information transfer. The accuracy of data entry directly influences the reliability of subsequent processes, highlighting its pivotal role in driving operational efficiency.
Integration with product lifecycle management
The seamless integration between BOM creation in ERP systems and product lifecycle management heralds a new era of interconnectedness. By linking BOM data with the product lifecycle, organizations can maintain a dynamic understanding of each product variant's evolution. This integration facilitates real-time updates to BOMs based on modifications in product designs or configurations. Such synchronization optimizes decision-making processes and ensures that the BOM accurately reflects the latest product specifications. The fusion of BOM creation with product lifecycle management fosters enhanced transparency in operations and cultivates a holistic approach to data management.
Version Control and Revisions
Tracking changes for compliance
In the realm of BOM management, tracking changes for compliance plays a fundamental role in maintaining regulatory standards and operational consistency. By monitoring and documenting alterations to the BOM over time, organizations can ensure compliance with industry regulations and internal quality standards. Tracking changes also enables the traceability of modifications, assisting in error identification and rectification. Compliance-driven change tracking instills a sense of order and accountability within the manufacturing process, offering clarity and structure amidst evolving operational landscapes.
Auditing capabilities
The auditing capabilities inherent in ERP systems empower organizations to conduct in-depth assessments of BOM revisions and historical data trails. By leveraging auditing tools, enterprises can scrutinize the evolution of BOMs, identify patterns of change, and evaluate the impact of revisions on overall operations. The ability to perform comprehensive audits not only enhances transparency but also instills confidence in the accuracy and integrity of the BOM data. Auditing capabilities serve as a safeguard against information discrepancies, providing a mechanism for continuous improvement and quality assurance within ERP-driven manufacturing environments.
Challenges in BOM Management
Understanding the complexities inherent in managing Bills of Material (BOMs) within Enterprise Resource Planning (ERP) systems is paramount to ensuring operational efficiency and product consistency. Addressing Challenges in BOM Management is essential as it directly impacts manufacturing processes and overall supply chain dynamics. One key consideration revolves around the dynamism of product configurations. This aspect emphasizes the constant evolution of product designs and features, necessitating seamless updates to BOMs. Adapting BOMs to align with changing product specifications requires meticulous attention to detail to avoid disruptions in manufacturing workflows. Companies must strategize on efficiently accommodating these updates within their ERP systems to maintain production continuity and product quality.
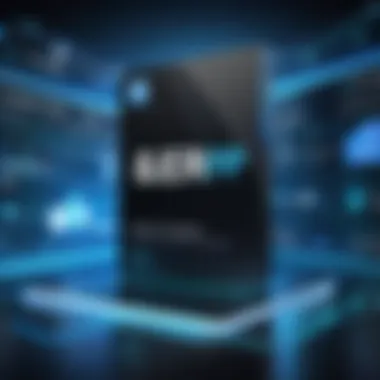
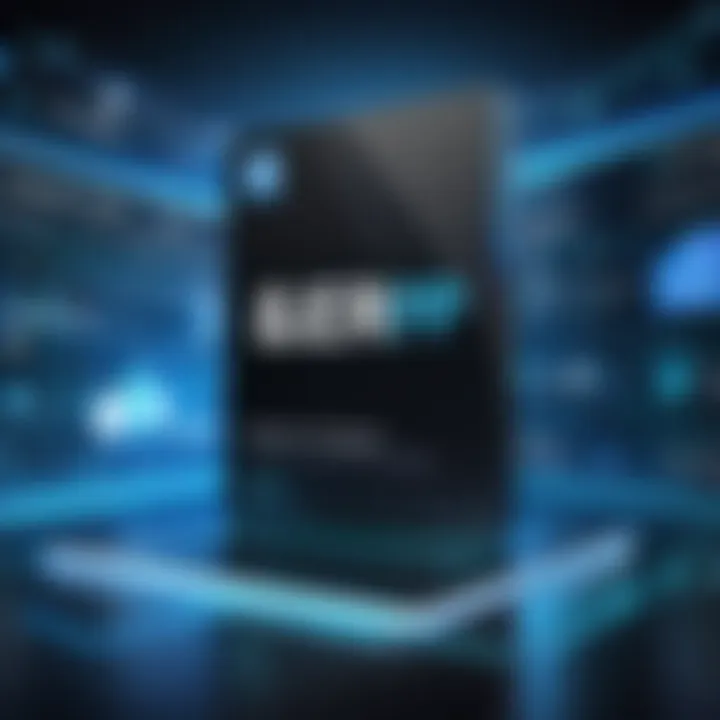
Another critical facet is the effect of BOM updates on the supply chain. This aspect underscores how alterations in BOMs can reverberate throughout the supply chain, influencing procurement, inventory management, and distribution strategies. Any modifications to BOMs can trigger a ripple effect on suppliers, production schedules, and cost structures. Therefore, comprehending the implications of BOM changes on the supply chain is imperative for fostering seamless coordination across all operational facets. While BOM updates can enhance product competitiveness and innovation, improperly managed alterations may lead to bottlenecks in the supply chain and customer dissatisfaction.
Complexity and Updates - Changing product configurations
Discussing the uniqueness of changing product configurations within BOMs delves into the iterative nature of product development. By capturing alterations in product attributes, such as dimensions, materials, or functionalities, changing product configurations epitomize the responsiveness of modern manufacturing to consumer demands. For instance, integrating new materials for enhanced product durability or upgrading features for increased functionality showcases the adaptability of companies in dynamic markets. The versatility of BOMs in accommodating these changes underscores their pivotal role in modern production environments. While managing changing product configurations can boost product differentiation and customer satisfaction, it necessitates robust systems for capturing, updating, and validating these modifications to maintain operational efficiency.
Complexity and Updates - Effect on supply chain
Assessing the effect of BOM modifications on the supply chain elucidates the interconnectedness of product data management and logistics. When BOM changes occur, they cascade across procurement, production planning, and inventory control processes, influencing resource allocation and order fulfillment. Disruptions in the supply chain may arise if these modifications are not harmonized promptly, resulting in delays, wastage, or inventory imbalances. Integrating BOM updates seamlessly into supply chain operations requires real-time visibility, collaborative platforms, and agile communication channels. While aligning BOM adjustments with supply chain activities can enhance responsiveness and adaptability, inadequate synchronization may lead to operational inefficiencies and revenue losses.
Integration with Other Modules - Linking BOM with inventory and procurement
Highlighting the integration of BOMs with inventory and procurement modules underscores the synergy between product design and material sourcing. By connecting BOM components with inventory levels and procurement schedules, companies optimize resource utilization and minimize stockouts. Real-time synchronization of BOM data with inventory databases enables proactive replenishment strategies and accurate demand forecasting. The seamless linkage between BOMs, inventory, and procurement streamlines material flow, reduces lead times, and mitigates inventory holding costs. Ensuring robust integration between these modules fortifies operational agility and cost efficiencies, positioning companies for competitive advantage in dynamic markets.
Integration with Other Modules - Ensuring data consistency
Examining the significance of data consistency in BOM management emphasizes the reliability and accuracy of product information across organizational functions. Maintaining data consistency between BOMs, inventory records, and production plans fosters harmonized decision-making and prevents discrepancies in material usage. By enforcing data integrity measures and validation protocols, companies uphold the quality and reliability of BOM data, enhancing process efficiency and compliance adherence. Consistent data integrity ensures seamless workflow orchestration and reduces errors in production execution, bolstering operational excellence and customer satisfaction.
Future Trends in BOM and ERP
In the ever-evolving realm of Enterprise Resource Planning (ERP) systems, the integration of innovative technologies plays a pivotal role in shaping future trends. As we delve into the enchanting realm of Future Trends in BOM and ERP in this comprehensive guide, it becomes evident that embracing advancements in technology is paramount for businesses striving to enhance operational efficiency and productivity. Exploring digital twin technology and the application of Artificial Intelligence (AI) and Machine Learning in BOM management unveils a new frontier of possibilities for optimizing manufacturing processes and product lifecycle management.
Digital Twin Technology
Simulating BOM digitally
The concept of simulating Bill of Material (BOM) digitally brings a groundbreaking revolution to traditional manufacturing practices. By replicating the product structure in a virtual environment, manufacturers gain unprecedented insight into product behavior, leading to improved decision-making and enhanced process efficiencies. The unique characteristic of digital twin technology lies in its ability to provide real-time feedback on product performance and facilitate predictive maintenance strategies, ultimately fine-tuning operational outcomes. Embracing digital twin technology in this narrative ushers in a new era of manufacturing precision and operational excellence.
Enhancing predictive maintenance
Enhancing predictive maintenance through digital twin simulations presents a paradigm shift in asset management strategies. By harnessing the power of data analytics and machine learning algorithms, organizations can proactively predict equipment failures and schedule maintenance activities, thereby minimizing downtime and optimizing resource allocation. The key characteristic of predictive maintenance lies in its ability to transform reactive maintenance practices into proactive, predictive models, fostering a culture of operational resilience and cost-effectiveness. While predictive maintenance offers significant advantages in optimizing production processes, challenges such as data complexity and algorithm accuracy should be diligently addressed to maximize its benefits in the context of this discourse.
AI and Machine Learning
Automating BOM optimization
Automating Bill of Material (BOM) optimization leverages the capabilities of AI and machine learning to streamline product development processes and enhance efficiency. By automating the selection of optimal components and materials based on predefined criteria, organizations can accelerate time-to-market and reduce production costs significantly. The key characteristic of BOM optimization automation is its ability to generate data-driven insights and recommendations, empowering decision-makers to make informed choices that drive operational excellence. While embracing automated BOM optimization is advantageous, considerations regarding data privacy and algorithm transparency must be addressed diligently within the framework of this discussion.
Predicting material shortages
Predicting material shortages through AI-driven algorithms offers a proactive approach to supply chain management and inventory control. By analyzing historical data and external factors, such as market trends and supplier performance, organizations can forecast and mitigate potential material shortages, ensuring uninterrupted production cycles and customer satisfaction. The key characteristic of material shortage prediction lies in its ability to optimize inventory levels, reduce excess stock, and minimize operational disruptions. While predictive analytics enhances supply chain resilience, challenges related to data accuracy and algorithm adaptability should be meticulously evaluated to harness its full potential in the context of this narrative.
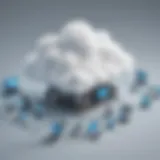
